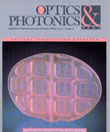
June 1990 Issue
- Optical fabrication and testing: a historical review
- International optical standards
- Automation in optics manufacturing
- Automated grinding
- Diamond machining
- Aspheric polishing with a stressed lap
- Testing aspheric surfaces
- Why measure MTF?
- When is a surface clean?
- Don't add more bureaucracy to standards, government told
- Kitchen chromatography
- Browse all Issues
Feature Articles
Optical fabrication and testing: a historical review
Optical fabrication and testing techniques are more than two thousand years old. It was discovered in 1927 that as far back as 1600 B.C., crystal magnifier lenses were made in Crete. Spectacles were invented around the year 1260. The next great advance came when the Dutch microscopist Anthony von Leewenhoek in 1719 made his own small magnifying lenses to examine microscopic objects. He discovered microorganisms with his small lenses. The manufacturing details until this time are not well known, and probably no attempt was made to test the quality of the surfaces.
by Daniel MalacaraInternational optical standards
In 1979, the International Standards Organization (ISO) formed a technical committee (TC172) to work on international standards for optics and optical instruments. As part of the committee's work, an optical drawing standard was developed and will be published in draft form before the end of the year. Because all the countries that have large optical industries are participating in writing these standards and the various delegations have reached a general consensus, it can be assumed that the standard will be adopted worldwide shortly after it is published in final form.
by Robert E. ParksAutomated grinding
Automated manufacturing processes have been the dream of production engineers for many years. In some fields—such as metal fabrication and automated assembly— the dream has become not just a reality, but a way of life. The optical sciences were quick to make use of computer technology when it was first available to perform the laborious ray trace calculations required in lens design. Only recently, however, have there been serious attempts to harness the computer aided manufacturing technologies for use in production optics shops to improve the American optical fabrication industry.
by Leland G. Atkinson IIIDiamond machining
The removal of material from a substrate using a single crystal natural diamond cutting tool has been experimented with in the United States for over 4 0 years. However, the most significant advances in this technology have taken place in the last decade. Today, single point diamond turning is recognized as a well established, cost effective, and repeatable manufacturing process. A wide variety of optical components, as well as mechanical components requiring micro-inch dimensional tolerances, are produced through single point diamond turning.
by Stephen C. HobertAspheric polishing with a stressed lap
The 1990s will see the construction of six to eight optical telescopes with effective diameters in the range 6.5 m to 16m, all larger than any existing telescope. The huge increases in light-gathering power have come about only through innovative mirror and telescope designs, for gravity does not allow a simple scaling up of existing 4-m-class telescopes. Thus, three new primary mirror concepts are being pursued vigorously: the segmented mirror of the 10m Keck Telescope,1 which consists of 36 thin 1.8-m segments of solid low-expansion glass ceramic; monolithic thin meniscus mirrors of the same material for the European Southern Observatory's 4 x 8.2-m Very Large Telescope2 and the 7.5 m Japanese National Large Telescope; and spin-cast borosilicate honeycomb mirrors up to 8 m in diameter for three projects involving the University of Arizona and two U.S. national telescope projects.
by H.M. MartinTesting aspheric surfaces
Advances in aspheric optical fabrication techniques are placing ever-increasing demands on the systems used to test these optics. With techniques such as single-point diamond turning and computer-controlled grinding and polishing, it is now possible to produce aspheric surfaces that cannot be easily or economically tested. And a surface that has not been properly tested is not really finished. Testing can be a substantial portion of the cost of producing an asphere.
by John E. GreivenkampWhy measure MTF?
Modulation Transfer Function (MTF) has been associated with measurement of performance of optical systems from the initial introduction of linear system analysis to this field. As the demand for higher quality, higher resolution optical systems has become prevalent, both designers and metrology scientists have begun investigating MTF as a mutual mode of quantifying the performance of optical systems. This article identifies the reasons for specification and measurement of MTF as a system characterization tool.
by Peter T. Carellas and Stephen D. FantoneDon't add more bureaucracy to standards, government told
Recently I was asked how one can specify the cleanliness level of a surface. After some thought, I had to admit I could not answer the question. It is almost as difficult as defining what a surface is. However, I may be able to shed a little light on the kinds of dirt one is likely to find on optical surfaces and ways to remove it.
by Robert E. ParksKitchen chromatography
Most primary school kids are taught that white light can be dispersed into a spectrum and that light of any spectral color can be synthesized by combining various intensities of red, blue, and green light. However, when kids mix paints they see that red paint mixed with green paint is not yellow; rather, it's olive-drab or brown.
by Susan Houde-Walter